As a plant manager, you’re always looking for ways to improve the efficiency of operations. One of the solutions you’ve been considering is switching from manual strapping tools to automated strapping systems.
You know these strapping equipment come with plenty of advantages. They can most certainly improve working conditions for your employees, but can they also make your work life easier?
Automated Strapping System Lower Worker Fatigue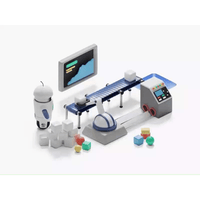
One of the biggest benefits of automated strapping system is their tireless work ethic. While human workers may get tired, your automatic strapping equipment can keep working at the same pace hour after hour.
As a result, your workers don’t need to work at breakneck speed to keep up with the shipping department’s busy schedule and high demand. The automated packaging machines can also take care of much of the heavy lifting.
The result is less worker fatigue. How does that benefit you, the plant manager? Less worker fatigue means more productive workers, for one.
It also means fewer mistakes and a lower rate of worker injury. With fewer injuries, you can spend less time filling out incident reports and wondering how you’re going to fill the schedule with a reduced workforce.
This benefit is two-fold: not only do workers get more done when they're not tired, but they're also less likely to make mistakes. This can save the company money in the long run, as well as increase morale among employees.
Automation Improves Productivity
Another major benefit of working with automated strapping system is improved productivity.
That’s good news for busy plants. High productivity is a must in order to keep up with demand and orders.
Working with automated packaging equipment also allows your team members to increase their productivity. Instead of spending all their time strapping packages, they could tackle other important tasks that usually fall by the wayside. They might be able to take more time to complete paperwork or to organize the floor. Maintenance, cleaning, and other jobs can now be prioritized to keep operations running smoothly.
Improve Quality over Manual Strapping
As mentioned, human workers tend to tire after long hours of repetitive movement. The longer they’re on the floor, the more likely it is they’re tired. Fatigue often leads to errors, as well as other issues.
These factors may lead to poor strapping jobs. Products might be damaged by straps that are too tight. Packages that are too loose may come undone or fall apart, which can also damage products.
You could end up spending time re-strapping packages that don’t meet quality standards, which means more time on strapping and lost productivity. The process of re-strapping could also cause delays in shipment and order fulfillment. Customers might demand a discount or cancel time-sensitive orders.
When you use a manual strapping method, you might also see that you end up handling more returns of damaged goods. To make up for the damaged product, you could need to write off additional inventory or offer discounts to buyers.
With automated strapping system, these situations are less common. The machine is less likely to make errors in tension or strap-sealing. Creates consistent tensions and seals every time.
With better quality strapping jobs, there is less risk of products being damaged or product coming undone. When the job is done right the first time, the product will be sent out on time too.
Automate Your Strapping for Peace of Mind
Automatic strappers don’t just benefit your workers. They often make the life of a plant manager much easier as well. From cost-savings and consistent quality to keeping your workers safer, the right strapping equipment could help you improve all your numbers.
If you’re ready to improve safety and streamline operations, get in touch with the experts. They can help you choose the right solution to protect both your product and your people.